Brazing Process
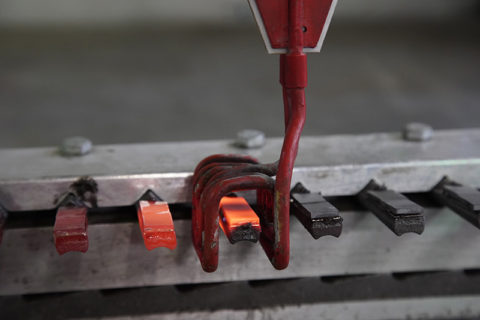
Alloys
Under the right conditions all common braze alloys from pure copper to silver alloys will readily wet cemented carbide surfaces. The most popular braze alloys consist of approximately 50% silver, and include alloys with cadmium (BAg-6), without cadmium (BAg-24), with manganese (BAg-22), and with tin (BAg-7). Thees alloys possess moderate melting points in the range of 1150 – 1300F and can be purchased in wire, rod, or ribbon form as a tri-metal braze in which a copper shim is “sandwiched” between two layers of silver alloy.
Brazing Material
For high temperature applications, copper is typically used as the brazing material. Although copper has a lower tensile strength than the silver alloys at room temperature, copper retains much of its strength for temperatures approaching 1000°F. If brazing is carried out in an oxidizing environment, borax is an effective flux for copper. Other high temperature brazes include high nickel alloys containing some chromium, boron, and silicon. These alloys flow at temperatures exceeding 1800°F. It should be noted that high brazing temperatures may cause grain growth, or other unwanted changes in the steel component.
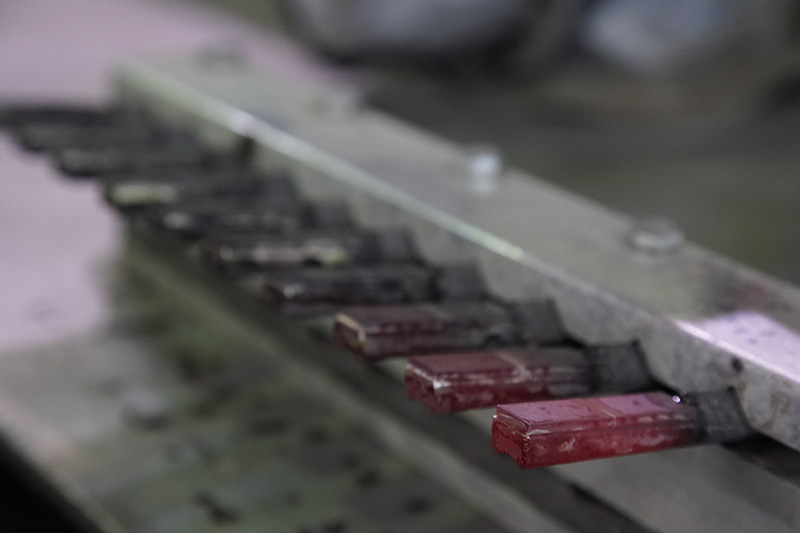
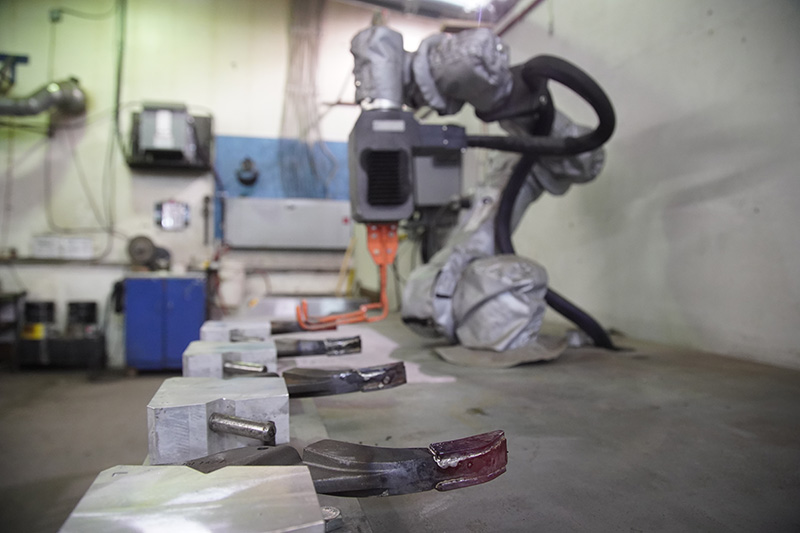
Flux
Fluxes are generally used in combination with the braze alloy to minimize the oxidation of surfaces to be joined during the heating of the assembly. “Black” flux is commonly used in combination with the silver alloys listed above, as it has a higher boron content and therefore is more effective at higher brazing temperatures.
Heating
Methods of heating the assembly to be brazed include hand torches, and high frequency induction coils. Torch flames should be somewhat reducing to minimize oxidation of component surfaces. It is important to heat the entire assembly uniformly to minimize thermal gradients and stresses and to reach, but not exceed the proper brazing temperature. Under-heated brazes will not melt and flow properly, while overheating may cause low boiling point constituents in the braze alloy to boil off. This alters the properties of the alloy and may result in entrapped gas bubbles in the braze joint. Any environmental factor that influences the rates of heating and cooling of the braze joint must be controlled to ensure that the quality of the braze joint does not vary.
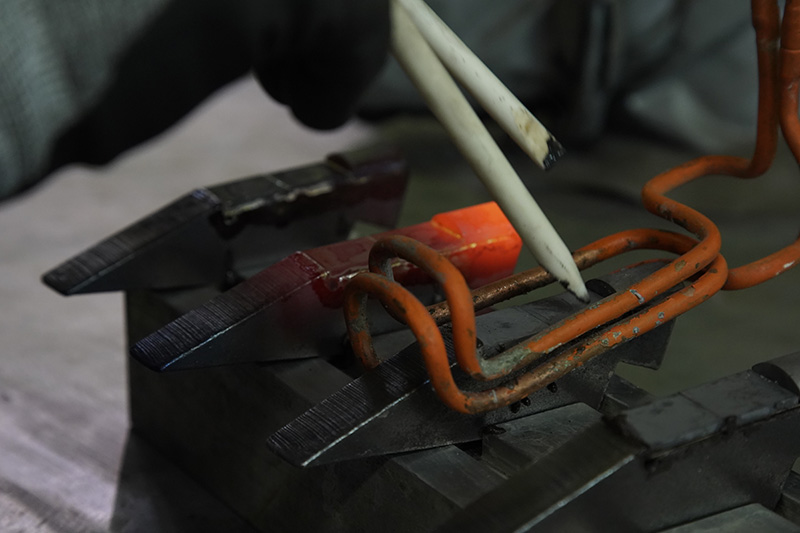